Centralt inom Lean är att skapa effektivitet genom korta ledtider. De korta ledtiderna ger i sin tur mindre lagerbindning, bättre leveransprecision samt att det bli enklare att upptäcka produktionsavvikelser. Korta ledtider gynnar leverantören, men det gynnar även kunden. Det finns alltså ett gemensamt intresse att få ner ledtider. Inom Lean ser man ofta ett problem i att få kunder att samarbeta i ledtidsprojekt. Jag menar dock att moderna inköpare som är inriktade på att utveckla försörjnings- och värdekedjan kommer att passa lean-leverantörer som handen i handsken.
En metod som används frekvent inom Lean är paretoanalys, ingen ’rocket science’ precis, men de använder den på lite annorlunda sätt. Låt mig ta ett exempel. Nedan har jag skissat upp ett enkelt ganttschema för en lite komplexare leverans:
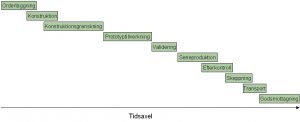
Ställer man istället tidselementen på högkant och sorterar dem i fallande ordning på klassiskt paretovis så får vi följande:
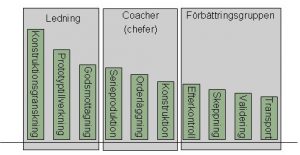
De flesta skulle nog, på klassiskt vis, ta russinen ur kakan, dvs de områden som har längst ledtid. De mindre lämnas utan åtgärd. Här har Lean en helt annat syn, inom Lean vill man att organisationen ska genomsyras av förbättringsarbete från produktion till styrelserum. Förbättringsgruppen sammansätts med personer från produktionen och de är dessa som leder förbättringsarbetet. Förbättringsgruppen ska sen coachas av chefer och ledning för att nå framåt i sin förbättringssträvan. De mindre åtgärderna löses bäst av förbättringsgruppen självt, men större åtgärder kan behövas lyftas till ledningen, eftersom de kanske fordrar investeringar i maskiner, lokaler och personal. De små åtgärderna är dock nog så viktiga, de gör att förbättringsgruppen känner att de har snabb framgång i några av sina åtgärder.
Ett sätt att klassificera förändringsåtgärder är genom s.k. PICK-chart (Possible, Implement, Challenge och Kill):
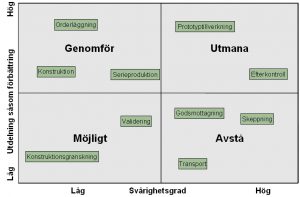
Detta hjälper förbättringsgruppen att klassificera förbättringsområdena så att det blir enklare att besluta om åtgärder.
Powerpoint:
PICK-chart mm